Mechanic
Monday, 18 August 2025
CAD vs Hand Drafting: Why Architects Prefer Digital! #sciencefather #res...
International Research Awards On Computer Aided Design In Mechanical Engineering
This paper aims to evaluate educators' and students’ preferences for either computer-aided design (CAD) or traditional hand drafting in working drawings coursework (assignments, term projects and exams). (1) Background: Working drawings are considered an advanced level of technical drawings for the architecture discipline.
Visit Our Website : cad.sciencefather.com
Nomination link : cad-conferences.sciencefather.com/award-nomination/?Category=Awards&rcategory=Awardee
Contact us : cadawards@sciencefather.com
Get Connected Here:
======================
Youtube : www.youtube.com/channel/UCGpONJQzsHCByPoa1ZeCPnA
Twitter : x.com/sophiai14453133
Pinterest : in.pinterest.com/mechanicsciencefather/
Instagram: instagram.com/mechcaddesigns/https://www.instagram.com/mechcaddesigns/
LinkedIn : www.linkedin.com/404/
Tumblr : https://www.tumblr.com/dashboard/hubs
#sciencefather #researchawards #professor #lecturerpoliticalscience
#scientist#scholar#Researcher #Analyst #engineers #technician #Coordinator #ResearchScientist #SeniorScientist#JuniorScientist #postdoctoralresearcher #LabTechnician #ResearchCoordinator #ResearchFellow #DataAnalyst #laboratorymanager #VisitingResearcher #3DPrinting #3DPrint #AdditiveManufacturing
Wednesday, 13 August 2025
How Robots Learn to Walk Smarter!#sciencefather #researchawards
International Research Awards On Computer Aided Design In Mechanical Engineering
Recent advancements in reinforcement learning (RL) and computational resources have demonstrated the efficacy of data-driven methodologies for robotic locomotion control and physical design optimization, providing a scalable alternative to traditional human-crafted design paradigms. However, existing co-design approaches face a critical challenge: the computational intractability of exploring high-dimensional design spaces, exacerbated by the resource-intensive nature of policy training and candidate design evaluations.
Visit Our Website : cad.sciencefather.com
Nomination link : cad-conferences.sciencefather.com/award-nomination/?Category=Awards&rcategory=Awardee
Contact us : cadawards@sciencefather.com
Get Connected Here:
======================
Youtube : www.youtube.com/channel/UCGpONJQzsHCByPoa1ZeCPnA
Twitter : x.com/sophiai14453133
Pinterest : in.pinterest.com/mechanicsciencefather/
Instagram: instagram.com/mechcaddesigns/https://www.instagram.com/mechcaddesigns/
LinkedIn : www.linkedin.com/404/
Tumblr : https://www.tumblr.com/dashboard/hubs
#sciencefather #researchawards #professor #lecturerpoliticalscience
#scientist#scholar#Researcher #Analyst #engineers #technician #Coordinator #ResearchScientist #SeniorScientist#JuniorScientist #postdoctoralresearcher #LabTechnician #ResearchCoordinator #ResearchFellow #DataAnalyst #laboratorymanager #VisitingResearcher #3DPrinting #3DPrint #AdditiveManufacturing
Supercharge VELMA: Auto-Init with HMS API & GDAL! #sciencefather #resear...
International Research Awards On Computer Aided Design In Mechanical Engineering
Continuous monitoring data required for performing environmental model simulations using gridded land surface models (LSMs) are often difficult to obtain and manage, making the modeling process challenging and prone to error.
Visit Our Website : cad.sciencefather.com
Nomination link : cad-conferences.sciencefather.com/award-nomination/?Category=Awards&rcategory=Awardee
Contact us : cadawards@sciencefather.com
Get Connected Here:
======================
Youtube : www.youtube.com/channel/UCGpONJQzsHCByPoa1ZeCPnA
Twitter : x.com/sophiai14453133
Pinterest : in.pinterest.com/mechanicsciencefather/
Instagram: instagram.com/mechcaddesigns/https://www.instagram.com/mechcaddesigns/
LinkedIn : www.linkedin.com/404/
Tumblr : https://www.tumblr.com/dashboard/hubs
#sciencefather #researchawards #professor #lecturerpoliticalscience
#scientist#scholar#Researcher #Analyst #engineers #technician #Coordinator #ResearchScientist #SeniorScientist#JuniorScientist #postdoctoralresearcher #LabTechnician #ResearchCoordinator #ResearchFellow #DataAnalyst #laboratorymanager #VisitingResearcher #3DPrinting #3DPrint #AdditiveManufacturing
Monday, 11 August 2025
Digital Twins: Engineering’s Next Big Leap! #sciencefather #researchawar...
International Research Awards On Computer Aided Design In Mechanical Engineering
A core function of digital twins in engineering is the visualization of the underlying product data to different stakeholders. Depending on the product lifecycle phase and stakeholder requirements, different visualizations are required which often results in laborious tasks not directly related to the product development.
Visit Our Website : cad.sciencefather.com
Nomination link : cad-conferences.sciencefather.com/award-nomination/?Category=Awards&rcategory=Awardee
Contact us : cadawards@sciencefather.com
Get Connected Here:
======================
Youtube : www.youtube.com/channel/UCGpONJQzsHCByPoa1ZeCPnA
Twitter : x.com/sophiai14453133
Pinterest : in.pinterest.com/mechanicsciencefather/
Instagram: instagram.com/mechcaddesigns/https://www.instagram.com/mechcaddesigns/
LinkedIn : www.linkedin.com/404/
Tumblr : https://www.tumblr.com/dashboard/hubs
#sciencefather #researchawards #professor #lecturerpoliticalscience
#scientist#scholar#Researcher #Analyst #engineers #technician #Coordinator #ResearchScientist #SeniorScientist#JuniorScientist #postdoctoralresearcher #LabTechnician #ResearchCoordinator #ResearchFellow #DataAnalyst #laboratorymanager #VisitingResearcher #3DPrinting #3DPrint #AdditiveManufacturing
How Machine Learning Supercharges Al–Li Alloys! #sciencefather #research...
International Research Awards On Computer Aided Design In Mechanical Engineering
To enhance the specific modulus of aerospace structural materials, this study employs machine learning methods to optimize the micro-alloying composition of Al–Li alloys. A total of 151 alloy composition-elastic modulus samples were analyzed.
Visit Our Website : cad.sciencefather.com
Nomination link : cad-conferences.sciencefather.com/award-nomination/?category=Awards&rcategory=Awardee
Contact us : cadawards@sciencefather.com
Get Connected Here:
======================
Youtube : www.youtube.com/channel/UCGpONJQzsHCByPoa1ZeCPnA
Twitter : x.com/sophiai14453133
Pinterest : in.pinterest.com/mechanicsciencefather/
Instagram: instagram.com/mechcaddesigns/https://www.instagram.com/mechcaddesigns/
LinkedIn : www.linkedin.com/404/
Tumblr : https://www.tumblr.com/dashboard/hubs
#sciencefather #researchawards #professor #lecturerpoliticalscience
#scientist#scholar#Researcher #Analyst #engineers #technician #Coordinator #ResearchScientist #SeniorScientist#JuniorScientist #postdoctoralresearcher #LabTechnician #ResearchCoordinator #ResearchFellow #DataAnalyst #laboratorymanager #VisitingResearcher #3DPrinting #3DPrint #AdditiveManufacturing
Saturday, 9 August 2025
How 3D CAD is Revolutionizing Car Design! #sciencefather #researchawards
International Research Awards On Computer Aided Design In Mechanical Engineering
This study systematically discusses the innovative application of 3D CAD technology in automotive machinery design, and constructs a closed-loop design system from parametric modeling to multi-physics simulation.
Visit Our Website : cad.sciencefather.com
Nomination link : cad-conferences.sciencefather.com/award-nomination/?ecategory=Awards&rcategory=Awardee
Contact us : cadawards@sciencefather.com
Get Connected Here:
======================
Youtube : www.youtube.com/channel/UCGpONJQzsHCByPoa1ZeCPnA
Twitter : x.com/sophiai14453133
Pinterest : in.pinterest.com/mechanicsciencefather/
Instagram: instagram.com/mechcaddesigns/https://www.instagram.com/mechcaddesigns/
LinkedIn : www.linkedin.com/404/
Tumblr : https://www.tumblr.com/dashboard/hubs
#sciencefather #researchawards #professor #lecturerpoliticalscience
#scientist#scholar#Researcher #Analyst #engineers #technician #Coordinator #ResearchScientist #SeniorScientist#JuniorScientist #postdoctoralresearcher #LabTechnician #ResearchCoordinator #ResearchFellow #DataAnalyst #laboratorymanager #VisitingResearcher #3DPrinting #3DPrint #AdditiveManufacturing
Thursday, 7 August 2025
VLM-MSGraph: Robots Get Smarter with Scene Graphs! #sciencefather #resea...
International Research Awards On Computer Aided Design In Mechanical Engineering
Intelligent robotic assembly is becoming a pivotal component of the manufacturing sector, driven by growing demands for flexibility, sustainability, and resilience. Robots in manufacturing environments need perception, decision-making, and manipulation skills to support the flexible production of diverse products.
Visit Our Website : cad.sciencefather.com
Nomination link : cad-conferences.sciencefather.com/award-nomination/?ecategory=Awards&rcategory=Awardee
Contact us : cadawards@sciencefather.com
Get Connected Here:
======================
Youtube : www.youtube.com/channel/UCGpONJQzsHCByPoa1ZeCPnA
Twitter : x.com/sophiai14453133
Pinterest : in.pinterest.com/mechanicsciencefather/
Instagram: instagram.com/mechcaddesigns/https://www.instagram.com/mechcaddesigns/
LinkedIn : www.linkedin.com/404/
Tumblr : https://www.tumblr.com/dashboard/hubs
#sciencefather #researchawards #professor #lecturerpoliticalscience
#scientist#scholar#Researcher #Analyst #engineers #technician #Coordinator #ResearchScientist #SeniorScientist#JuniorScientist #postdoctoralresearcher #LabTechnician #ResearchCoordinator #ResearchFellow #DataAnalyst #laboratorymanager #VisitingResearcher #3DPrinting #3DPrint #AdditiveManufacturing
Subscribe to:
Posts (Atom)
CAD vs Hand Drafting: Why Architects Prefer Digital! #sciencefather #res...
International Research Awards On Computer Aided Design In Mechanical Engineering This paper aims to evaluate educators' and students’...
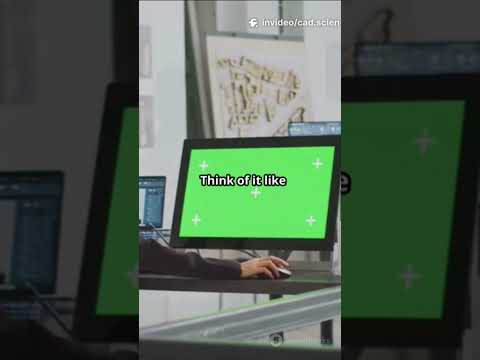
-
CNC MACHINING CNC 101: The term CNC stands for 'computer numerical control', and the CNC machining definition is that it is a su...
-
Gears play a critical role in mechanical engineering, serving as essential components in various machines and mechanisms to transmit power...
-
Mechanical Engineering is considered an essential discipline is known for applying engineering principles to various life walks, including d...